The wool debate: Environmental Effects of worsted versus woolen processing – insights for sustainable fashion. When fiber fineness is synonym with luxury but carries environmental concerns
The climate impact of wool depends from the length of its fibers: The research from Polytechnic University of Turin and the Italian textile company Manteco
A recent life cycle assessment focusing on the environmental effects of wool asserts itself as the inaugural endeavour to underscore and quantify the notably distinct climate impacts between longer wool fibers (worsted system) and shorter fibers (woollen system).
The primary objective of the study was to delineate the environmental impacts of 1 kg of raw wool across various fibers. Previous impact assessments had presumed that woollen and worsted fibers had identical impacts—an assumption contradicted by this study’s findings. The investigation revealed that worsted wool, commonly employed in the creation of tailored garments such as suits, accounted for 78 – 97 kg CO2 eq/kg, whereas shorter fibers utilized in woollen processing resulted in a considerably lower carbon footprint of 25 – 30 kg CO2 eq/kg.
Published in the peer-reviewed Journal of Cleaner Production, the study was conducted by researchers from the Polytechnic University of Turin and the Italian textile company Manteco, which also provided funding for the research.
Worsted and woollen: processing wool in two different ways create different environmental impacts
The International Wool Textile organization asserts that depending on its length and fineness, wool fiber can be transformed into a diverse array of woven and knitted fabrics. The process of wool, often considered one of the most sustainable raw materials, begins with sheep shearing, yielding both long and short fibers. Initially, the wool undergoes scouring, wherein it is washed with hot water and detergent to eliminate impurities like dirt, suint salts, and non-wool protein material.
Subsequently, the fibers are dried and subjected to carding, a mechanical procedure that cleans, separates, and blends them. This sets the stage for two distinct paths in wool processing: combing. Here, wool fibers encounter a pinned cylinder that straightens the long fibers while eliminating the shorter ones, constituting about 10% of the total quantity. These shorter fibers, referred to as “noils” or “blouses,” are not discarded; rather, they undergo the woollen processing. Meanwhile, the long and uniform fibers proceed to the worsting process.
Woollen yarn, crafted from the shorter fibers of a sheep’s fleece – about raw materials
Woollen yarn, crafted from the shorter fibers of a sheep’s fleece, tends to be thick, soft, lightweight, and imbued with airiness. Its fibers are loosely bound and spun with limited twist, one of the raw materials, ideal for crafting warm winter wear (like jackets, sweaters, skirts, and blankets) and bulky, heavyweight woven or knitted garments. Typically, one pound of woollen yarn can be spun into a maximum of 54 hanks, each measuring 256 yards.
On the other hand, worsted yarn is a premium-grade wool yarn known for producing fine fabrics. It is spun from the long-staple pasture wool of sheep breeds like Teeswaters, Old Leicester Longwool, and Romney Marsh. The worsted process involves combing out the short hairs from the fiber, resulting in a smoother yarn. The fabric made from worsted yarn is commonly used as one of the raw materials in tailored garments such as suits, as well as carpets, clothing, hosiery, gloves, and baize. It possesses a soft texture and fuzzy surface, lacking shine or sheen, resistant to creasing, and heavier and bulkier compared to worsteds.
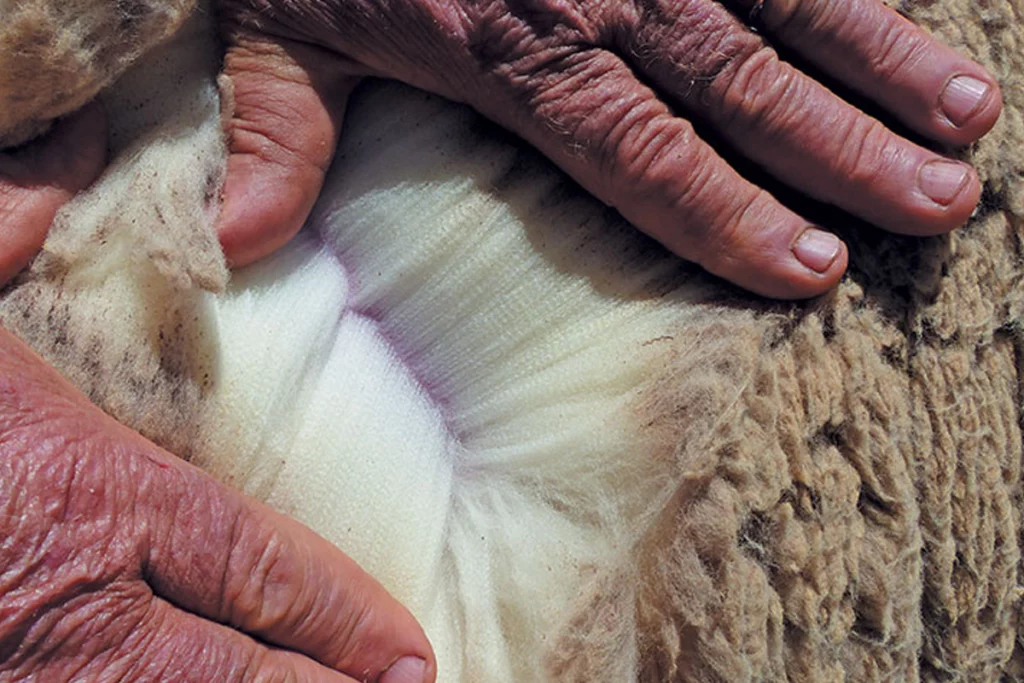
The disparity between woollen and worsted yarn: Wool’s sustainable manufacturing process
The initial stages in the wool manufacturing process involve grazing, shearing, and scouring to obtain wool free from grease and dirt. Typically, this phase yields the clean fleece, containing the longest and cleanest fibers, clean belly wool, clean oddments, pieces, and locks or lower quality parts, wool grease (lanolin), and waste (approximately 21% of the total mass). Sometimes, a subsequent carbonization process is necessary for belly wool and oddments to remove vegetable matter. Carbonization entails treatment with sulfuric acid, which adheres to the vegetable matters, followed by drying to make it brittle and easier to remove. Scouring and eventual carbonization yield clean fleece, and clean (or carbonized) belly wool and oddments, pieces, and locks. Clean fleece, with longer and finer fibers, undergoes transformation into very fine yarn through the worsted processing system. Conversely, clean/carbonized belly wool and oddments, along with other fibers discarded from the worsted processing system, are turned into coarser yarns via the woollen processing system. In both processes, fibers undergo carding, a mechanical process that disentangles fibers and reduces impurities to produce a continuous web for subsequent production stages.
The worsted processing is considered to be a less sustainable manufacturing process: carding primarily produces long staple fibers (around 97% in mass), with discarded fibers termed burry wool (or burs, about 3%). These may be carbonized in some cases and incorporated into the woollen processing system. Long staple fibers are then gilled and combed, generally involving three gilling operations before and two after combing. Gilling aligns fibers and produces a sliver with uniform weight, while combing straightens fibers and removes short fibers and foreign matter. Noils, about 10% of the combed wool, are utilized in the woollen processing after potential carbonization. The combed long fibers, after further gilling, form continuous worsted slivers (called tops), sometimes breaking into open tops for woollen processing. Dyeing is typically performed on bumps, with subsequent combing to remove remaining short fibers (about 2%) for woollen processing. Drafting, reducing top thickness, transforms it into sliver, composed of drawing and roving passages. Discarded fibers (spinning soft waste) from drafting are generally sent to woollen processing. Finally, sliver undergoes spinning to produce very fine yarn, with discarded fibers (spinning hard waste, about 3% in mass) typically recycled.
Raw Materials – The woollen process, suitable for shorter fiber
The woollen process, suitable for shorter fibers, usually produces coarser yarn compared to worsted processing. Blending with longer natural or man-made fibers is often necessary to achieve acceptable yarn strength when processing very short fibers. Belly wool and oddments can be used in woollen processing, potentially carbonized. Additionally, short fibers discarded from worsted processing (burs, open tops, noils, and spinning soft waste) undergo carding and spinning processes in the woollen system.
The disparity between woollen and worsted yarn lies in several factors. Woollen yarn is spun from wool fibers with a length of short fibers of 1-3” and a diameter of medium or coarse. It is processed with washing, scouring, and carding. Woollen yarns are carded only, less twisted, and therefore weaker in strength. They result in bulky, uneven yarn with low to medium twist and lower tensile strength, woven with plain or twill weave, resulting in less compact, less durable fabric. They offer insulation due to trapped air but are less crease-resistant and durable. Woollen fibers offer superior warmth but lack luster and durability.
From an environmental standpoint, woollen yarn is made following a more sustainable manufacturing process. Conversely, worsted yarn is spun from wool fibers with a length longer than 3” and a finer diameter. It undergoes washing, scouring, carding, combing, and drawing processes. Worsted yarns are carded and combed, highly twisted, and stronger. They result in fine, smooth, even yarn with tighter twist and higher tensile strength. Worsted fabrics are mainly woven with twill weave, creating a closer, more durable structure. They are less insulating but crease-resistant and more durable than woollens. Worsted wool wrinkles less, retains creases and shape, and develops a shiny patina with wear.
Wool processing in worsted and woollen systems: carbon footprint variation
The study presented by Polytechnic University of Turin and Manteco presents an overview of the potential impacts of 1 kg of various intermediate products in worsted processing, including clean fleece with vegetable matters, top and bumps, combed dyed tops, not dyed sliver, dyed sliver, and very fine yarn, dyed and not dyed. Notably, dyed fine yarn stands out for its higher potential impacts as the final product, totaling 97.2 kg CO2 eq/kg. The grazing phase is the prime contributor, representing 89% of the total impact, while other transformations collectively contribute for 11%.
As for the potential impacts of 1 kg of intermediate products in woollen processing, they generally show lower potential impacts than worsted products. Notably, open tops, belly wool (with vegetable matter or carbonized), and spinning soft waste demonstrate the highest potential impacts, indicating relatively high economic value compared to other fibers used in woollen processing.
ReviWool® noils, Manteco’s low-impact virgin wool
Moreover, a contribution analysis on a woollen product, the ReviWool® noils, Manteco’s low-impact virgin wool, reveals that the grazing phase accounts for the highest share of impacts (95% of the total). However, compared to combed fibers, its impact is lower (about 66% less), reflecting the dominance of worsted products in driving the wool sector’s materials and resource utilization.
Additionally, the analysis on wool sensitivity highlights the contribution and variability of the grazing phase to the total impact. It is suggested that companies seeking to evaluate specific wool products should identify the sources of greasy wool and related grazing phase impacts. A further examination on sensitivity examines the influence of physiological variations in co-product ratios on the final impact, indicating limited impact on climate change. Maximizing the yield of long fibers results in the best environmental performance across both worsted and woollen products.
Loro Piana Record Bale: celebrating the record-breaking Merino wool from Australia and New Zealand measuring 10.6 microns
In the continuous research for finer and higher-quality wool, Loro Piana celebrates its longstanding relationship with the top Merino wool producers rewarding them annually. In its 23rd edition, Loro Piana Record Bale, recognizes farms that produce the finest and most prestigious wool in the world. This year winners’ were Pyrenees Park farm in Australia, owned by Pamela and Robert Sandlant, which received the recognition for the sixth consecutive year, and Visuela Farm in New Zealand, owned by Barrie and Yvonne Payne.
The two farms delivered wool bales with thicknesses of 10.6 and 11.1 microns respectively. To fully grasp the level of the excellence achieved, consider that a human hair measures 80 microns, a unit of measurement for fiber fineness, equivalent to one-thousandth of a millimeter.
Loro Piana, a maison specializing in artisanal craftsmanship of cashmere
Since 1997, Loro Piana, a maison specializing in artisanal craftsmanship of cashmere, vicuña, and extra-fine Merino wool, has been challenging breeders to produce increasingly finer wool. The first winning bale back then measured just over 13 microns. Meanwhile, the fiber has been refined by almost 25%.
There are benefits connected to wearing garments made of the finest fabric: the fiber’s structure, akin to a microscopic spring, enables the creation of crease-resistant fabrics with a fluid drape, capable of accommodating body movements due to the material’s intrinsic elasticity. Merino wool acts as a second skin, ensuring breathability and adapting to changes in body heat compared to fluctuations in external temperature.
From approximately 150 meters of Record Bale, no more than 40 bespoke garments are crafted, made at Loro Piana’s ateliers and in some selected tailoring houses worldwide.
Manteco
Manteco is a textile company founded in 1943, in Tuscany, Italy. They are specialized in high-quality fabrics and jerseys made with animal and vegetal fibers following sustainable manufacturing practices
Loro Piana
Loro Piana is an Italian company specialized in clothing and textile products made from the rarest raw materials, claiming to be the world’s largest cashmere manufacturer